Did you know that the BBA was originally created out of a need for tighter regulations and quality standards within the construction industry?
In the 60s, many construction industry failures were attributed to innovative building materials not being accurately described by the manufacturer, which caused huge problems for the construction industry itself, not to mention the ability to set the right quality standard to reduce the risk of building failures without stifling innovation. But innovative materials, by definition, are not covered by standards – so how do you know how a product will perform?
Fast-forward to today and the BBA is providing the construction industry with independent and authoritative information about products and has been for over 50 years. But what the BBA does that many other testing and certification bodies don’t do, is go beyond in order to mitigate risk throughout the supply chain; providing information and guidance on where a product can be used and for how long, based on independent and authoritative information.
The BBA continues to build specialist Technical Excellence departments that are responsible for knowing the most up to date, state-of-the-art assessment methodology standards, building regulations and compliance in specific areas of constriction. The BBA works with its clients, helping them identify and comply to the relevant building regulations applicable to their products and systems.
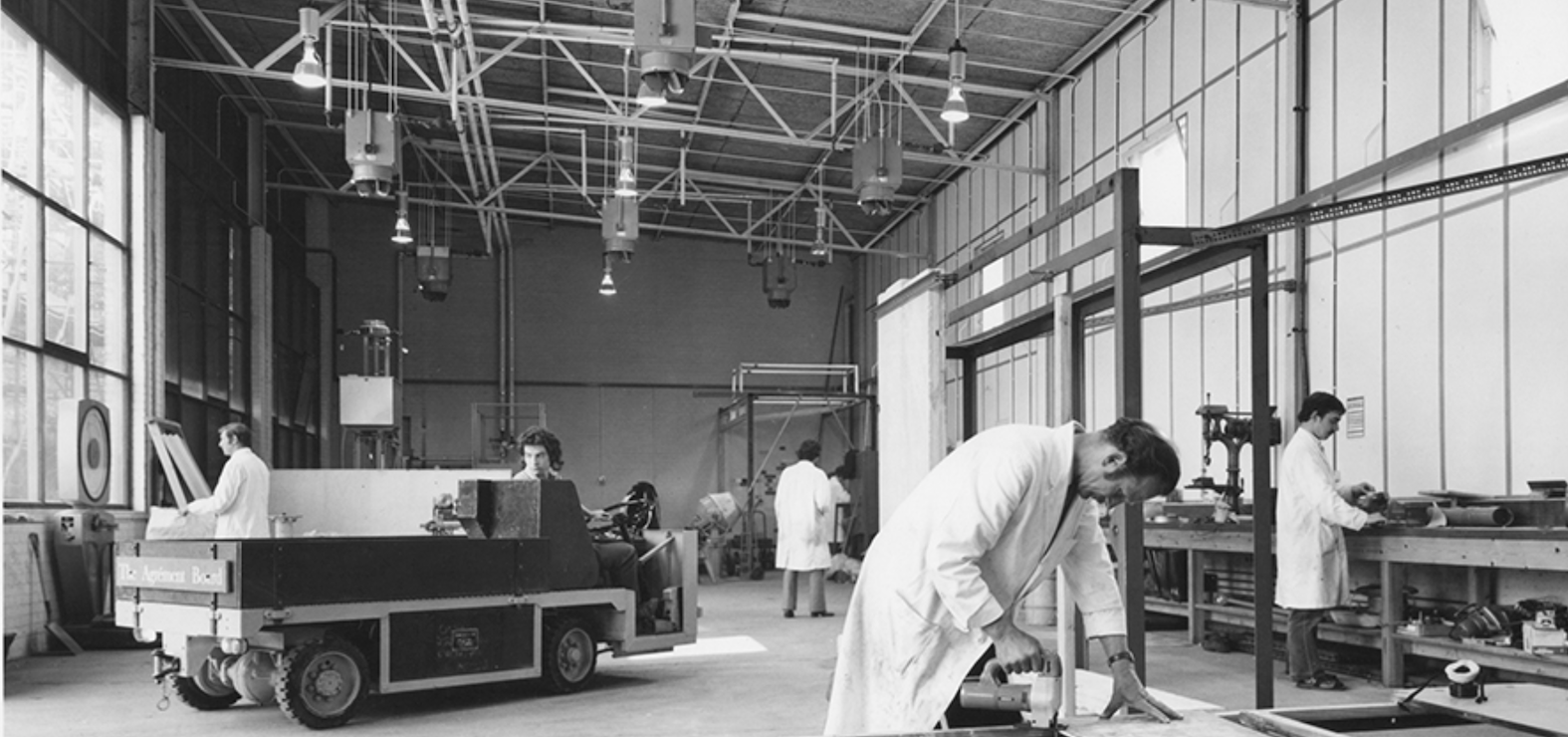
What does this mean for manufacturers?
For manufacturers, the BBA applies a level playing field, challenging the industry to adhere to the same level of performance; or risk not conforming to industry or self-imposed standards. This means that poorer performing materials are highlighted through the comparisons made between specific product information; information which is both reliable and impartial.
The Supply Chain Benefit?
With BBA Agrément Certification, specifiers rely on independently validated data, and not something simply published by the manufacturer without verification or authentication, providing the information required and a sense-check as to the viability of that product being selected and used for a specific building or purpose. IN doing this the BBA is helping to shape the decision-making process and ensure the necessary conformity to building regulations and other legislative processes.
Test
The BBA is far more than just Agrément certification however. Take the Test Department for example, which aims to provide clients with the confidence that through our rigorous testing and expertise, their product will be challenged to reach the required standard for its given use, thus mitigating their risk within the intended market.
The BBA’s Test offering is an industry leader in the standards for testing. The BBA is accredited by UKAS for a set of essential tests and, for the tests that are not covered under this accreditation, the BBA ensures a standard that exceeds that of UKAS. This means that regardless of client requirements, testing is of the highest standard.
As a UKAS-accredited body, the BBA also undergoes its own set of annual checks through audits by UKAS, providing even greater assurance that the benefits that clients receive, are those that adhere to the strictest of guidelines and that best practices continue to be established.
Partnering with our clients means that the BBA helps to mitigate risk during a product’s development by providing testing at any stage of its lifecycle; be it pre-launch, during development or on-going testing once a product is on the market. In addition, bespoke testing can be done to meet whatever the client’s needs are at any given time. This specificity means even for products that are innovative or similar to existing ones with small variations, the BBA’s test facilities can provide the testing required that suits and supports the clients product development goals.
Through the broad and extensive experience and expertise across many products sectors, which includes materials, physics, engineering and more, the BBA Test department knows the right questions to ask clients so that the right information is obtained about their products and the testing requirements needed which helps mitigate financial and technical risks are established.
Audit and Inspection (A&I)
The BBA certification process has been created to not only test and verify fitness-for-purpose, but to enable manufacturers to continue to subscribe to the same product quality around which their certification is based. That’s why the certification process is also supported by ongoing audits and inspections to ensure the products continue to be relevant. The audit process requires several visits to a manufacturer’s factory, where the production method is assessed, ensuring that the process is compliant and adheres to the same production methods used to initially gain certification, and that any changes are reviewed accordingly.
Audit – Manufacturing
Assessing the production lifecycle of the intended product at the preliminary stage, adds to the quality and integrity of the product itself. By carrying out an audit correctly and with vigilance, we help reduce the overall risk of a poorly manufactured, and therefore unsuitable, product being introduced into the market.
Inspection – Installation
BBA inspections assess the installation of a product. At this point, the product has already gone through the rigorous production assessment of the audit team, ensuring that the product is of sound quality and suitability. However, the inspection arm goes further to ensure that the product is installed correctly in a manner it should be through best practices.
Prior to installation, the inspection team will assess the condition of the product and ascertain general information around the way it has been stored, mixed and used relating to the type of product. The inspection process also subsequently checks the physical installation of the product as to where it should be applied and fitted in accordance with the manufacturer’s guidelines to ensure that the installation process adheres to the same commitment to quality as the product certification itself.
Warranties and Insurances
Finally, clients can and do issue product or system warranties, or insurances off the back of some of the inspections carried out by the BBA. Although this is more of an indemnification for any potential risk, the decisions to allow for any warranty or insurance, shows a commitment to quality, and a degree of confidence in the process, which indicates a level of low risk.
And all of this, from the BBAs own early inception structured to help mitigate risks within the construction supply chain and create a safer world for all stakeholders.
Share This Story, Choose Your Platform!
Related News
Did you know that the BBA was originally created out of a need for tighter regulations and quality standards within the construction industry?
In the 60s, many construction industry failures were attributed to innovative building materials not being accurately described by the manufacturer, which caused huge problems for the construction industry itself, not to mention the ability to set the right quality standard to reduce the risk of building failures without stifling innovation. But innovative materials, by definition, are not covered by standards – so how do you know how a product will perform?
Fast-forward to today and the BBA is providing the construction industry with independent and authoritative information about products and has been for over 50 years. But what the BBA does that many other testing and certification bodies don’t do, is go beyond in order to mitigate risk throughout the supply chain; providing information and guidance on where a product can be used and for how long, based on independent and authoritative information.
The BBA continues to build specialist Technical Excellence departments that are responsible for knowing the most up to date, state-of-the-art assessment methodology standards, building regulations and compliance in specific areas of constriction. The BBA works with its clients, helping them identify and comply to the relevant building regulations applicable to their products and systems.
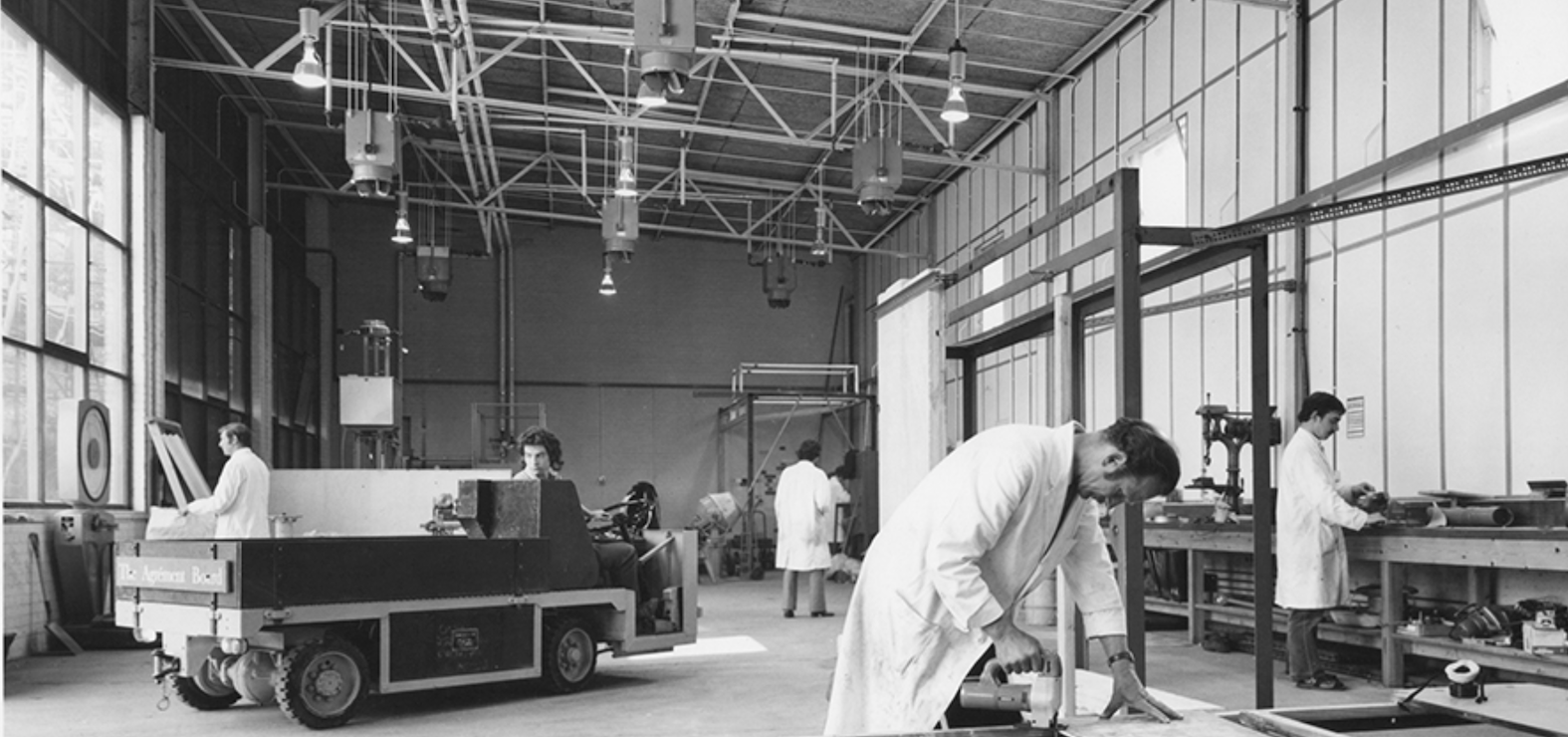
What does this mean for manufacturers?
For manufacturers, the BBA applies a level playing field, challenging the industry to adhere to the same level of performance; or risk not conforming to industry or self-imposed standards. This means that poorer performing materials are highlighted through the comparisons made between specific product information; information which is both reliable and impartial.
The Supply Chain Benefit?
With BBA Agrément Certification, specifiers rely on independently validated data, and not something simply published by the manufacturer without verification or authentication, providing the information required and a sense-check as to the viability of that product being selected and used for a specific building or purpose. IN doing this the BBA is helping to shape the decision-making process and ensure the necessary conformity to building regulations and other legislative processes.
Test
The BBA is far more than just Agrément certification however. Take the Test Department for example, which aims to provide clients with the confidence that through our rigorous testing and expertise, their product will be challenged to reach the required standard for its given use, thus mitigating their risk within the intended market.
The BBA’s Test offering is an industry leader in the standards for testing. The BBA is accredited by UKAS for a set of essential tests and, for the tests that are not covered under this accreditation, the BBA ensures a standard that exceeds that of UKAS. This means that regardless of client requirements, testing is of the highest standard.
As a UKAS-accredited body, the BBA also undergoes its own set of annual checks through audits by UKAS, providing even greater assurance that the benefits that clients receive, are those that adhere to the strictest of guidelines and that best practices continue to be established.
Partnering with our clients means that the BBA helps to mitigate risk during a product’s development by providing testing at any stage of its lifecycle; be it pre-launch, during development or on-going testing once a product is on the market. In addition, bespoke testing can be done to meet whatever the client’s needs are at any given time. This specificity means even for products that are innovative or similar to existing ones with small variations, the BBA’s test facilities can provide the testing required that suits and supports the clients product development goals.
Through the broad and extensive experience and expertise across many products sectors, which includes materials, physics, engineering and more, the BBA Test department knows the right questions to ask clients so that the right information is obtained about their products and the testing requirements needed which helps mitigate financial and technical risks are established.
Audit and Inspection (A&I)
The BBA certification process has been created to not only test and verify fitness-for-purpose, but to enable manufacturers to continue to subscribe to the same product quality around which their certification is based. That’s why the certification process is also supported by ongoing audits and inspections to ensure the products continue to be relevant. The audit process requires several visits to a manufacturer’s factory, where the production method is assessed, ensuring that the process is compliant and adheres to the same production methods used to initially gain certification, and that any changes are reviewed accordingly.
Audit – Manufacturing
Assessing the production lifecycle of the intended product at the preliminary stage, adds to the quality and integrity of the product itself. By carrying out an audit correctly and with vigilance, we help reduce the overall risk of a poorly manufactured, and therefore unsuitable, product being introduced into the market.
Inspection – Installation
BBA inspections assess the installation of a product. At this point, the product has already gone through the rigorous production assessment of the audit team, ensuring that the product is of sound quality and suitability. However, the inspection arm goes further to ensure that the product is installed correctly in a manner it should be through best practices.
Prior to installation, the inspection team will assess the condition of the product and ascertain general information around the way it has been stored, mixed and used relating to the type of product. The inspection process also subsequently checks the physical installation of the product as to where it should be applied and fitted in accordance with the manufacturer’s guidelines to ensure that the installation process adheres to the same commitment to quality as the product certification itself.
Warranties and Insurances
Finally, clients can and do issue product or system warranties, or insurances off the back of some of the inspections carried out by the BBA. Although this is more of an indemnification for any potential risk, the decisions to allow for any warranty or insurance, shows a commitment to quality, and a degree of confidence in the process, which indicates a level of low risk.
And all of this, from the BBAs own early inception structured to help mitigate risks within the construction supply chain and create a safer world for all stakeholders.
Share This Story, Choose Your Platform!
Related News
Get in touch
Please complete the form below and we will contact you as soon as possible.
To help us to respond to your inquiry as quickly as possible, we have put a handy list of our services below.